
Dental CAD/CAM systems have the potential to minimize inaccuracies in technique and reduce hazards of infectious cross-contamination associated with conventional multistage fabrication of indirect restorations. CAD/CAM systems offer automation of fabrication procedures with increased quality in a shorter period of time. The current milling center systems are Procera® (Nobel Biocare USA, LLC, Yorba Linda, CA), Lava™ (3M ESPE, St Paul, MN), and TurboDent (U-Best Dental Technology, Anaheim, CA).ĬAD/CAM technology provides several advantages for dental laboratories. Dental laboratories can either send working casts to an authorized milling center for scanning, design, and milling, or purchase a scanner and send data files to the milling center for milling and finishing. The milling center systems offer outsourcing services and allow laboratories entry into CAD/CAM technology at a level that is most comfortable. The laboratory systems, such as CEREC inLab®, DCS Precident (Popp Dental Laboratory, Inc, Greendale, WI), Cercon® (DENTSPLY Ceramco, York, PA), Everest® (KaVo Dental Corp, Lake Zurich, IL), and DentaCAD (Hint-ELs® Canada Inc, Ontario), are comprised of a scanner, a CAD design unit, and a CAM mill unit for generating restorations on-site. The in-office systems include CEREC® 3D and E4D Dentist™ (D4D Technologies LLC, Dallas, TX). Integration of these technologic advances has resulted in the introduction of three categories of highly sophisticated CAD/CAM systems: in-office systems, laboratory-based systems, and milling center systems. Another vital factor has been the development of alumina (aluminum oxide) and zirconia (zirconium oxide) ceramic materials, which possess excellent machinability and physical strength. Replacement of conventional milling discs with a variety of diamond burs has resulted in major improvements in milling technology.
#CAD CAM SYSTEM SERIES#
A series of methods have been used to collect three-dimensional (3D) data of the prepared tooth, from optical cameras to contact digitization to and laser scanning. 2 This requirement demands that CAD/CAM systems have a very accurate data collection technique, sufficient computing power to process and design complex restorations, and a very precise milling system.ĭuring the past two decades, exciting new developments have led to the success of contemporary dental CAD/CAM technology. The American Dental Association specifies that a dental restoration must fit its abutment within 50 μm. The first commercially viable dental CAD/CAM system was CEREC® (Sirona Dental Systems, LLC, Charlotte, NC), developed by Mormann and Brandestini. However, this system was not successful in the dental market because of its complexity and cost. 1 In 1984, Duret developed the Duret system, which was later marketed as the Sopha Bioconcept system (Sopha Bioconcept, Inc, Los Angeles, CA), demonstrating the ability of CAD/CAM to generate single-unit, full-coverage restorations.
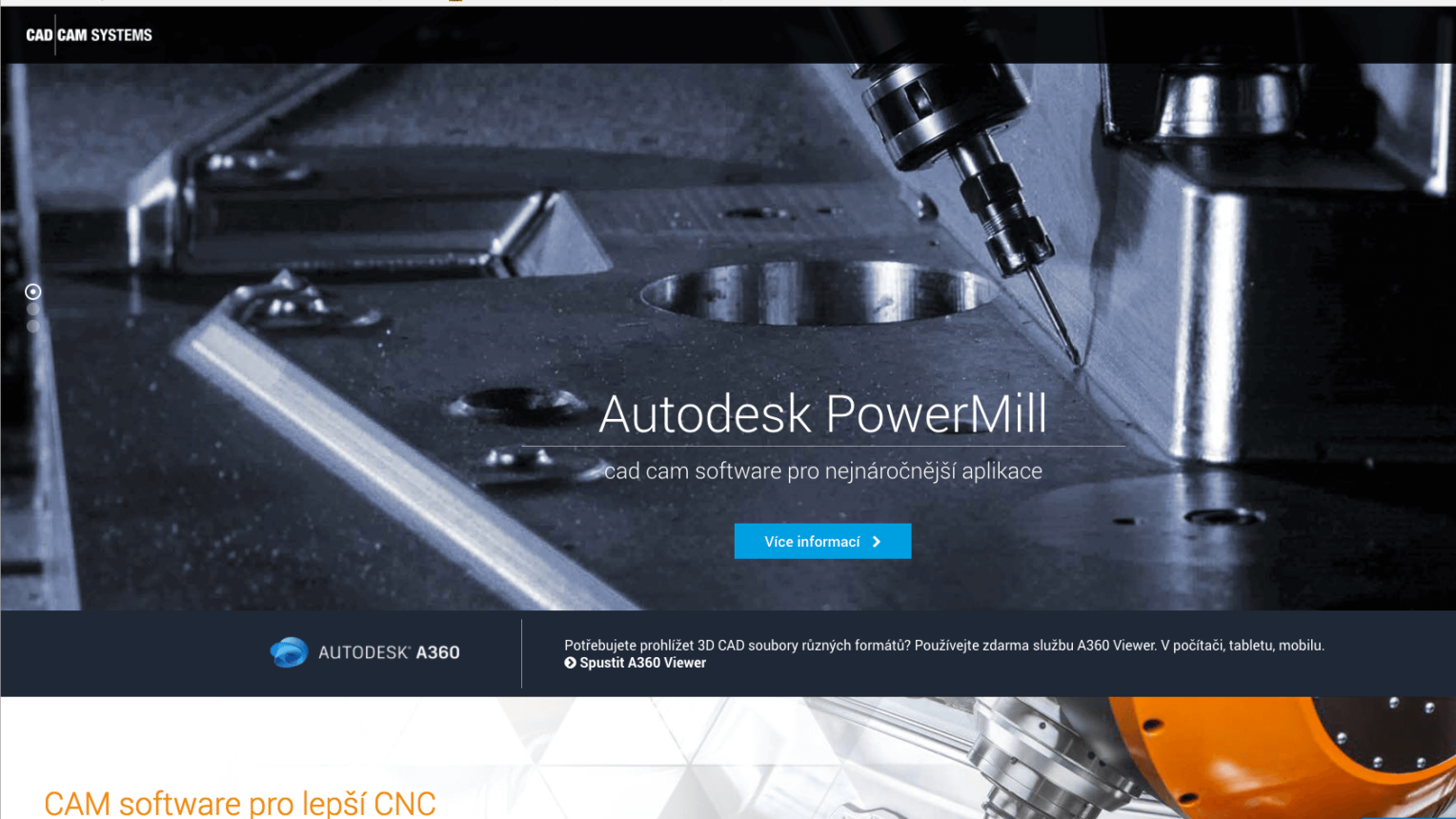
Young and Altschuler first introduced the idea of using optical instrumentation to develop an intraoral grid-surface mapping system in 1977.

The earliest attempt to apply CAD/CAM technology to dentistry began in the 1970s with John Young, DDS, and Bruce Altschuler, DDS, in the United States, Francois Duret, DDS, MD, in France, and Werner Mormann, BMD, DDS, and Marco Brandestini, PhD, in Switzerland. These systems have been in general use in industry for many years, but dental CAD/CAM applications were not available until the 1980s. Research data and clinical studies are presented to substantiate the clinical performance of these systems.Ĭomputer-aided design (CAD) and computer-aided manufacture (CAM) technologic systems use computers to collect information, and design, and manufacture a wide range of products. Operational components, methodologies, and restorative materials used with common CAD/CAM systems are discussed. This article provides an overview of the development of various CAD/CAM systems. Several highly sophisticated in-office and laboratory CAD/CAM systems have been introduced or are under development. ABSTRACT: In the last two decades, exciting new developments in dental materials and computer technology have led to the success of contemporary dental computer-aided design/computer-aided manufacture (CAD/CAM) technology.
